En el diseño eléctrico y la producción, la exactitud y la precisión son esenciales para mantener los proyectos dentro de plazo y presupuesto. El más mínimo descuido puede dar lugar a problemas que se propagan en un efecto cascada por todo el proceso de producción, lo que provoca retrasos y un aumento de los costes. Al detectar los errores en una fase temprana, los fabricantes pueden rectificar los fallos de diseño mucho antes de que lleguen a la planta de producción.
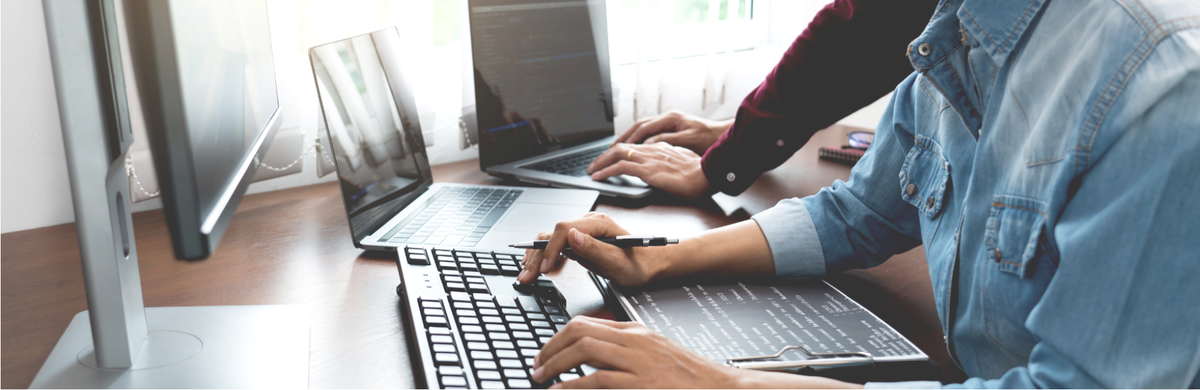
¿Cuáles son los problemas de diseño más comunes que provocan errores eléctricos?
Aunque existen muchos fallos comunes en el diseño eléctrico que pueden repercutir en el coste, la viabilidad y la duración de los proyectos, la buena noticia es que un diseño avanzado asistido por ordenador puede ayudar a superarlos.
A continuación se enumeran algunos de los problemas de diseño más comunes:
- Componentes que no caben en el espacio designado para el armario.
- Alambres o cables que no caben dentro de los conductos de cableado.
- Basarse en diseños obsoletos copiando y pegando de proyectos anteriores, lo que genera información obsoleta y confusión en el área de producción.
- Múltiples versiones del mismo diseño sin un proceso claro de gestión de las revisiones, lo que genera confusión e ineficacia.
- Interrupción de la comunicación entre los equipos de ingeniería de diseño, adquisiciones y producción, lo que provoca un derroche innecesario de recursos.
- Duplicación de las etiquetas de los componentes, lo que provoca pedidos de piezas erróneos y retrasos prolongados.
- Números de pieza inexactos o incorrectos que causan estragos en las búsquedas manuales y en los plazos de los proyectos.
- Falta de sincronización entre las modificaciones de los esquemas y los planos de disposición de los paneles.
- Números de cable que faltan.
- Información de perforación incorrecta.
Descárgate nuestra guía gratuita y domina el diseño eléctrico
El problema de los errores de diseño simples
Los errores de diseño eléctrico, cuando se pasan por alto, pueden tener implicaciones de gran alcance. En lugar de limitarse a la fase de diseño, pueden impregnar el proceso de producción, lo que afecta a la eficacia, los plazos y los presupuestos. Por tanto, resulta fundamental detectar y corregir de forma proactiva los errores de diseño antes de que se conviertan en problemas más graves.
Si se siguen las mejores prácticas de diseño eléctrico avanzado o se emplean trucos para mejorar la eficiencia de los diseños eléctricos, los equipos de ingeniería y diseño pueden reducir considerablemente la posibilidad de errores. Una metodología de diseño sólida, unida a unos procesos exhaustivos de validación y revisión, proporciona una protección vital frente a errores costosos. El poder de la detección precoz de errores reside en su capacidad no solo para prevenirlos, sino también para mantener un flujo fluido e ininterrumpido a lo largo de todo el ciclo de vida, desde el diseño hasta la producción.